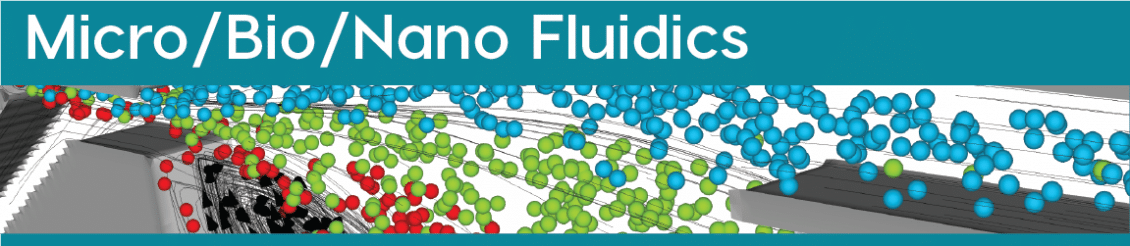
Integrating mechanical, fluidic, optical, and electronic functionality in a very small package, modern microfluidic devices have important advantages over their conventional counterparts in terms of cost, scale and their ability to integrate directly into larger systems. 3D modeling and visualization are efficient tools for providing rich quantitative analyses, substantially reducing research time, design and production costs. Micro, bio and nano fluidics can be easily and accurately simulated with FLOW-3D’s free surface and multi-fluid modeling capabilities. We invite you to explore the various applications and processes that can be better understood through simulation.
Micro/bio/nano Fluidics Playlist
In this 1-D microfluidic palette simulation using FLOW-3D, a clean decoupling of the convective cells from the main central microchannel can be seen be through the plotted streamlines. The streamlines are all restrained to the convection units only and not even a single one leaks out into the microchannel, indicating excellent decoupling of convection and diffusion. The evolution of source concentration can be seen in the plot, which becomes visibly constant by the end of the animation.
Ubiquitous gravity can be used for sorting micro particles in microfluidic devices. When gravity acts perpendicular to the motion of the particles, the particles settle down at a velocity dependent on their radius. Additionally, the motion of the particles is influenced by the hydrodynamic effects originating from the difference between the density of the particles, the density of the fluid and the viscosity of the fluid. The image below shows the gravity sorting technique schematic.
In this video of hydrodynamic microfluidic separation, we see particle sorting based on varying diameters. The technique works on the principle that a particle will follow a streamline. Particles with the smallest diameter (red) get easily carried towards the top of the constriction and hence at the divergence follow the streamlines that diverge upwards. Particles with the largest diameter (blue) stay their course and move towards the bottom of the constriction. On exiting the constriction, these particles follow the streamlines that diverge downwards.
Thermocapillary actuation on an array of 4 heaters activated in a sequential order.
This FLOW-3D simulation shows a comparison between a fully-wetted and a partially-wetted surface. As expected, the fully-wetted surface makes the droplet flatter (and more spread out) than in the partially-wetted surface. As the heaters are activated one at a time, the droplet is propelled towards a colder area. It can be seen that the fully-wetting surface loses more fluid volume by the end of the simulation as more fluid is left behind. Therefore, partially-wetting surface is a more preferable option to reduce fluid loss. In both cases, the droplet is forced to stay in the middle because of the central hydrophilic strip surrounded by a hydrophobic surface.
To add some measure of control and reproducibility to continuous inkjets, a prescribed perturbation is typically applied at the jet origin that ensures a breakup of the jet into a series of regularly spaced droplets.
FLOW-3D simulation showing the mixing of the fluids coming in from two inlets. Iso-surfaces are plotted at the inlet, curved section and the outlet to highlight the formation of vortices and evolution of mixing over the length of the microchannel.
Simulation of whole blood flow through a modified V-groove channel using capillary forces.
FLOW-3D animation highlighting the partial reversal of 3 droplets that get visually mixed and then un-mixed at the end of simulation. The partial reversibility is attained because of the highly laminar flow.
Patterned surfaces are used to transport fluids in lab-on-a-chip, bioassays, microreactors and, chemical and biological sensing. In this example, surface tension is used to manipulate fluid flows in micro channels to create patterned flows.
Simulation of a pneumatic latching valve used in a microfluidic demultiplexer. The system evolves from an initial open state to a closed state.
This simulation shows a temperature rise of the fluid due to Joule heating. The temperature rises to 500 degree Celsius by the end of the simulation. FLOW-3D captures the fluid flow physics of a di-electric fluid inside an electric field as seen in the right half of the simulation. Streamlines have been plotted using FlowSight in order to visualize the fluid flow and are colored by electric field magnitude. Over time, clearly visible distinct circulation cells are formed in the fluid as the polarized particles are moved around by the electric field. The top left plot in the simulation shows the electric field magnitude contours.
Two droplets are merged when force is exerted on the di-electiric droplets due to the presence of a non-uniform electric field. This phenomenon is called dielectrophoresis and can be accurately simulated using FLOW-3D.
This FLOW-3D simulation illustrates the application of electro-osmosis for use with micro-pumps. By creating a series of deep slots in a microchannel, and then applying a potential across the channel, fluid flow can be controlled in a MEMS-scale pump. By adjusting the applied potential, the flow rate can be controlled. Visualized with FlowSight, FLOW-3D‘s state-of the-art postprocessor.
FLOW-3D flow simulation of droplet formation in a 3D T-Junction device. Simulation by Flow Science, post-processed with FlowSight, FLOW-3D‘s state-of-the-art postprocessor.
The animation shows the separation of four particle species based on the relative densities. The separation is driven by the curvature in the microchannel geometry. FLOW-3D‘s particle model is used to simulate particle movement and assign them mass and diameter.
FLOW-3D simulation showing the formation of L2 lenses. L2 lenses are used in optofluidics for focusing light through the principle of refraction. This animation shows variable lens profile formation for different core inlet flow rates. Since the left and the right cladding inlet flow rates are fixed to the same value, only bi-convex (symmetrical) lenses are formed.
Continuous inkjet printing results comparison of an input pressure pulse with constant amplitude versus one with random fluctuations in the input pressure pulse.
Fluidic oscillators are flow control devices that work based on the Coanda effect and generate spatially oscillating bursts (or jets) of fluid. These oscillators have no moving parts and are thus rugged and maintenance-free devices. The most common application of fluidic oscillators include windscreen cleaning devices on cars or trucks, fluidic amplifiers, flow separation control and drag reduction, controlling actions, flow meters, mixing or separation of chemical components, micro-bubble, and micro-drops generating, noise control, injector nozzles, and different sensors. This FLOW-3D simulation shows the internal flow of a fluidic oscillator along with the sweeping jet in the external flow field.
This FLOW-3D simulation of a 2-D microfluidic palette demonstrates a spatio-temporal control on the generated gradients. The source and sink are rotated at an angular velocity. Also, after every t seconds, the active access port is deactivated and the next port is turned on. To see the live status of the diffusion inside the chamber, three line probes are placed in the simulation (marked in red, blue and black, respectively, in the bottom right window of the simulation). Read the blog.
This FLOW-3D simulation shows the kinetic energy fluctuations for a microfluidic compact disc rotating at 7000 rpm. At this rotation speed, compared to the 1000 rpm speed (https://youtu.be/stAYg1nAr2E), steady state is reached faster but with rapidly fluctuating water levels. Read the blog.
Electrowetting is a technique used to change the apparent contact angle of a dielectric fluid under the influence of electric potential. In this example, the fluid is originally hydrophobic and beads on the surface. However, when a 50V potential difference is applied, the fluid is forced to wet the surface becoming hydrophilic.
Animation showing the formation of biconvex shape lens using a core flow (black fluid) rate of 3 mL/h and cladding flow (white) rates of 7 mL/h.
Flow focusing is a microfluidics technique to generate droplets or bubbles using hydrodynamics. In this video, FLOW-3D is used to simulate the flow focusing process.
This simulation is looking at droplet ejection of a piezo driven inkjet. These drop-on-demand (DoD) printheads are used for a variety of applications from conventional printing processes to additive manufacturing processes such as binder jetting and material deposition. FLOW-3D allows for analysis of how system parameters and fluid rheology affect droplet velocities, uniformity, and overall consistency in the printed image or part.
Customer Case Studies
Challenges, smaller than can be seen by the naked eye, are what our customers using FLOW-3D to model microfluidics applications face every day. FLOW-3D allows these engineers and scientists to model what they cannot replicate in the laboratory, to validate life-saving medical devices, study inkjet formation and in some cases, model the naked eye. Sometimes the smallest problems are the biggest to solve… but FLOW-3D can help.